A structured way to plan work,
understand and operate technology, and communicate effectively
Many
people apply the Input-Process-Output
model without being aware of it. Using the model deliberately can be very
helpful for:
·
planning work
· understanding and operating technology
·
communicating effectively
·
structuring training
Work
and technical processes control changes
to achieve the desired results. The following diagram shows the three stages of
the change process:

As
a generality, work and technical processes are used to change materials to
produce a desired result (e.g., reshape metal, bake a cake, assemble an
appliance, separate hydrocarbons into various components, create a chemical
change). Generally, the quality of the output product remains constant.
Sometimes a change in the quality of the input materials creates the need to
adjust the work or technical process to achieve the desired output.
Input,
process, and output can be thought of as a continuous loop.
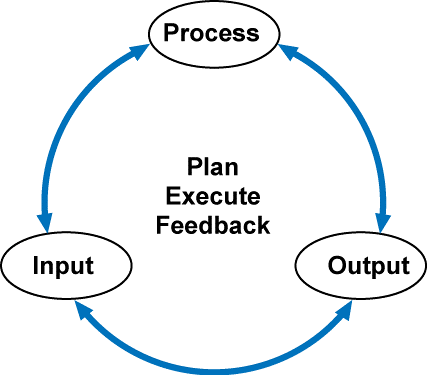
One
can start at any point in the loop and go in either direction to plan, execute,
and get feedback. Starting with output is a natural starting point because the
objective or result must be understood before considering how to achieve those
results. After having used the strategy to initially think though the work, a
different starting point and sequence can be used to get a better understanding
of a specific concern. The goal is to continually refine and improve safety,
efficiency, and cost-effectiveness in achieving the desired results.
Within a given set of roles and responsibilities, one must identify the variables
(e.g., quantity, composition, shape, pressure, temperature) that must be monitored,
controlled, or responded to achieve the desirable output. For example:
·
input
variables define the quality of the materials used
·
process
variables of personal action, tools, and equipment
that create the change
·
output variables define the
quality of the product or results
Each variable must be measurable either using numerical units and ratios or
non-numerical units. Examples of numerical units and ratios are 3600
revolutions per minute, 130 degrees Fahrenheit, 325 centimeters long, 2 parts
water to 5 parts of pulp. Examples of non-numerical measurements are the water
appears clear and put just enough force on the board to get a clean cut but not
so much to overload the motor.
To
control the technology and make decisions, one needs to know the
characteristics of the variables as shown in the matrix below.
VARIABLE
|
Static
|
Dynamic
|
Controllable
|
static
&
controllable
|
dynamic
&
controllable
|
Non-controllable
|
static
&
non-controllable
|
dynamic
&
non-controllable
|
Knowing
whether an equipment or material variable can change and whether or not the
change can be controlled is very helpful in doing jobs well and responding
effectively to changes. One must also understand the cause(s) or reason(s) for
changes and how changes can impact PEMEO (defined in a previous post). Asking
questions about the variables can be very useful for performing work and
understanding and controlling technology effectively.

Using
the input-process-output model is an excellent way to organize ideas to
communicate effectively as a trainer or supervisor. The model can help to
organize content in training documents such as self-instructional modules. The input-process-output
model can provide an overview in the introduction. For example, when explaining
what a piece of equipment does, a brief statement such as the following could
be used:
·
Trees are fed into a chipper which reduces the trees to chips
to produce mulch (input-process-output)
·
Mulch is produced by making chips out of trees (output-process-input)
·
The chipper slices trees into chips to produce mulch (process-input-output)
The
detailed content can then be organized in the same order presented in the
introduction.
The
books EquipThink and MatThink provide detailed information
about thinking strategies to plan work, do work, use technology and materials effectively,
efficiently, and safely, and to make effective decisions. Using thinking
strategies contributes to exemplary employee performance which, in turn, can
improve job and corporate performance. The books use an educational design and
have exercises to apply the thinking to the world of work.
Do
you use the input-process-output model when thinking about work or operating
and maintaining technology? Do you think this model is a useful thinking
strategy in your personal life? Do you think that the input-process-output
model is useful for communicating how technology works and to structure
training?
Gordon
Shand is President of HDC Human Development Consultants Ltd. He has 35 years of
experience designing and developing educational and training programs that have
excellent practical value and contribute to the customer’s business success. www.hdc.ca